Semi-autonomous 4×4 rover Mark I
September 21, 2019In January 2017 (the spring before I started at Missouri S&T), I decided that I wanted to take a stab at designing and building a simple semi-autonomous rover. It didn’t have to be anything fancy, I just wanted to try it to see if I could do it. Since I didn’t really have a mission for the rover, or specific task that I wanted it to perform, I spent some time and thought up a core set of functionality constraints and made an “operational wishlist” of other stuff that would be cool to have but not truly necessary.
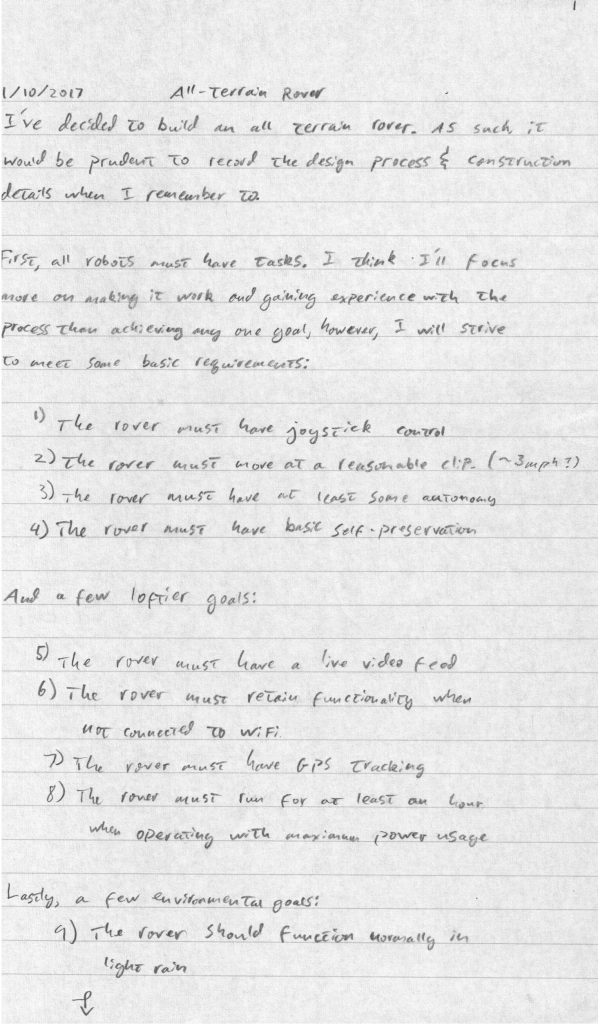
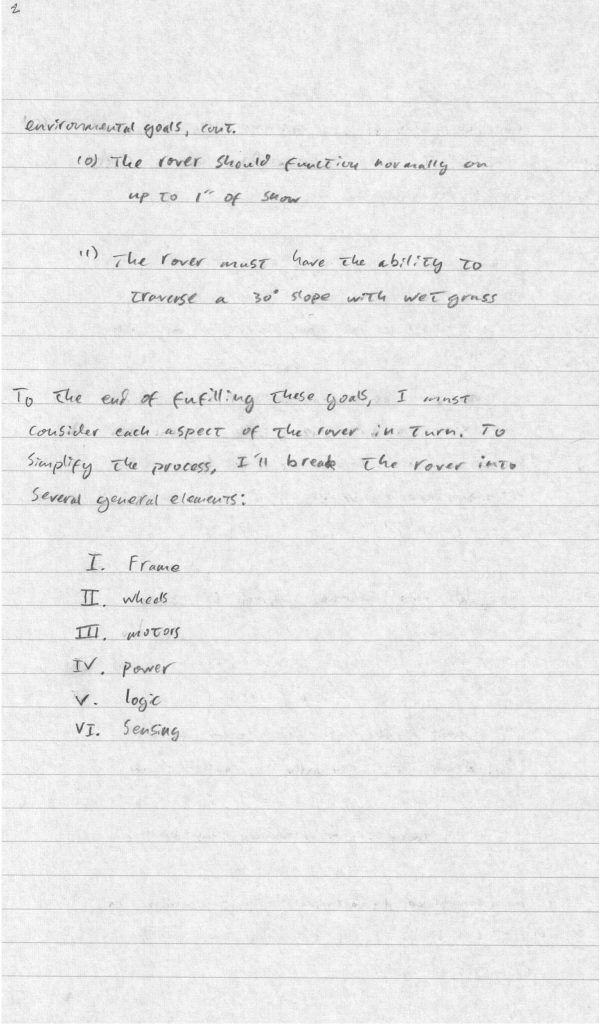
As a starting point, I chose to design the body of the rover first. The frame would be the thing that everything else would attach to, so it made sense to me to design it first. Once I had a serviceable rover body, I would worry about fitting everything that I needed into that volume.
To simplify the process a bit, I more fully defined the requirements and constraints for the frame. By doing this, I aimed to gain a clearer picture of the solution space. To make it manageable, I also broke the frame down into several sub-sections that I would consider individually: The main section, The access hatch(es), and the leg struts.
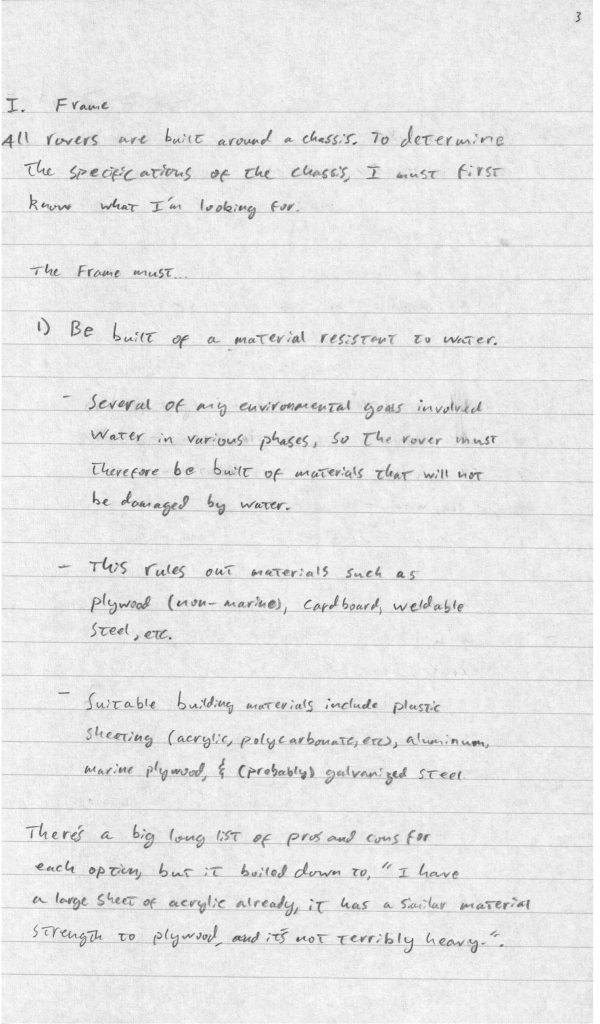
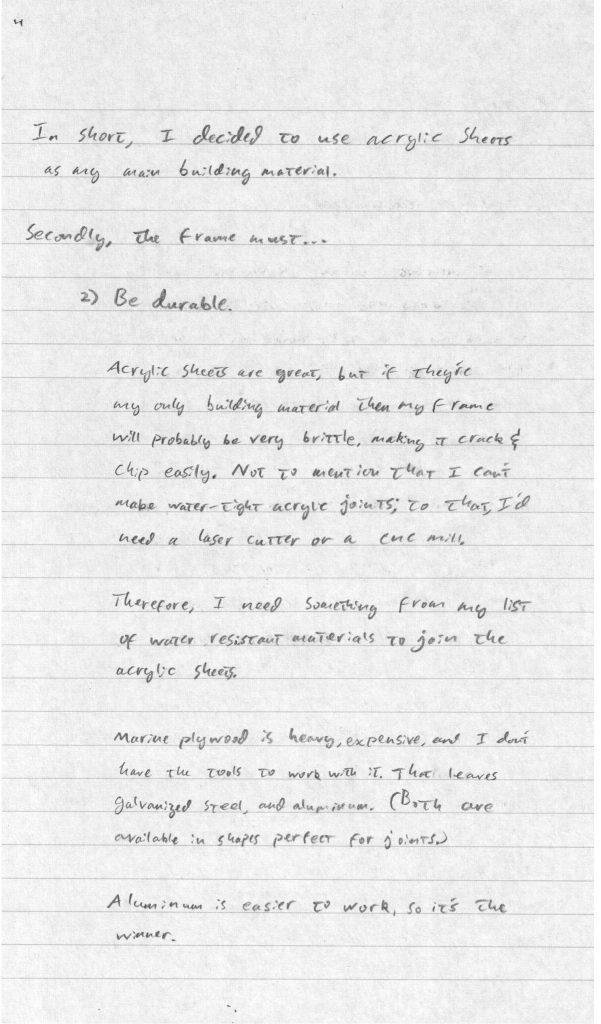
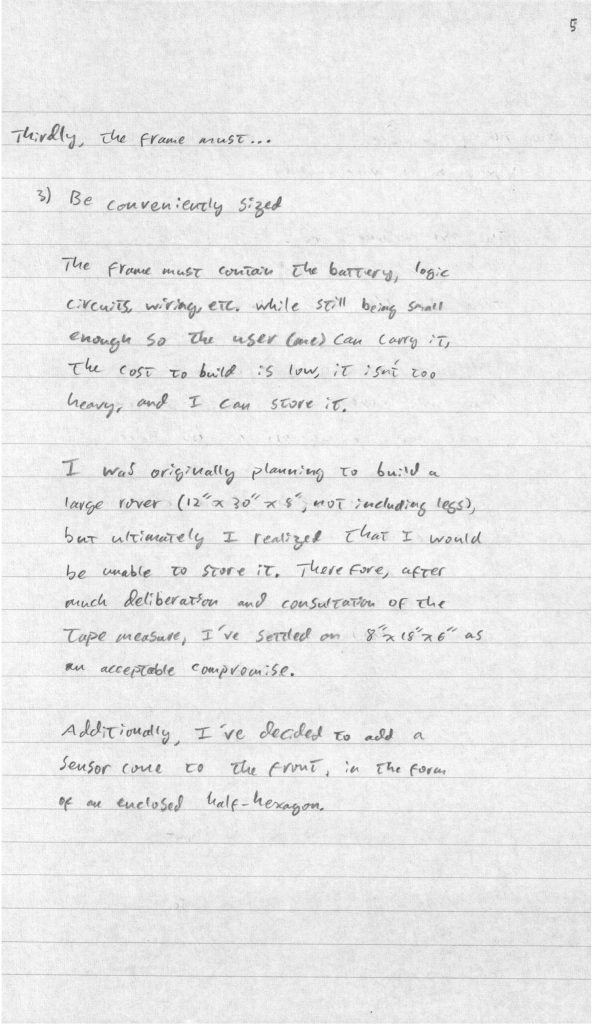
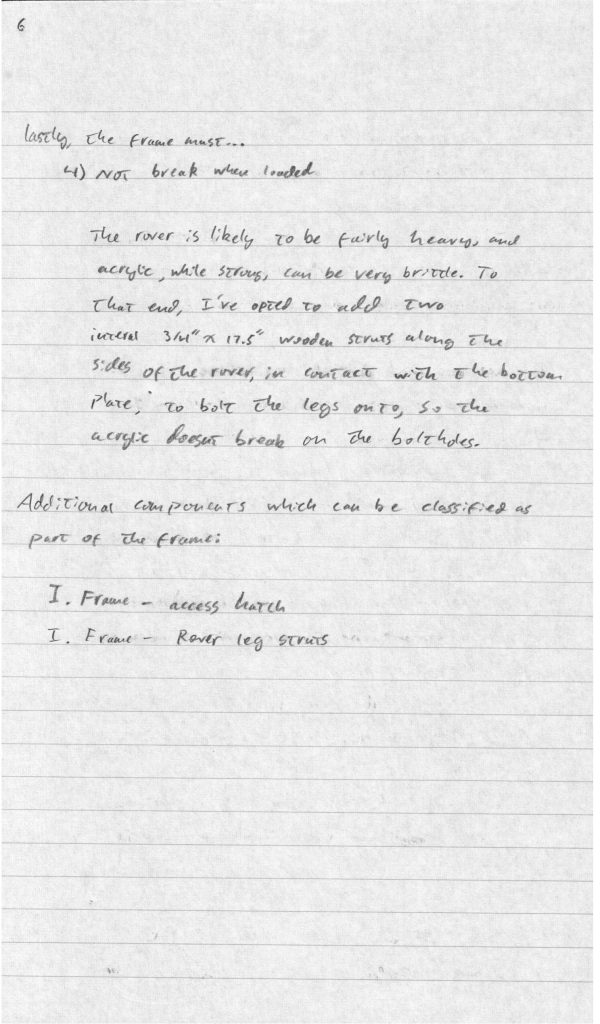
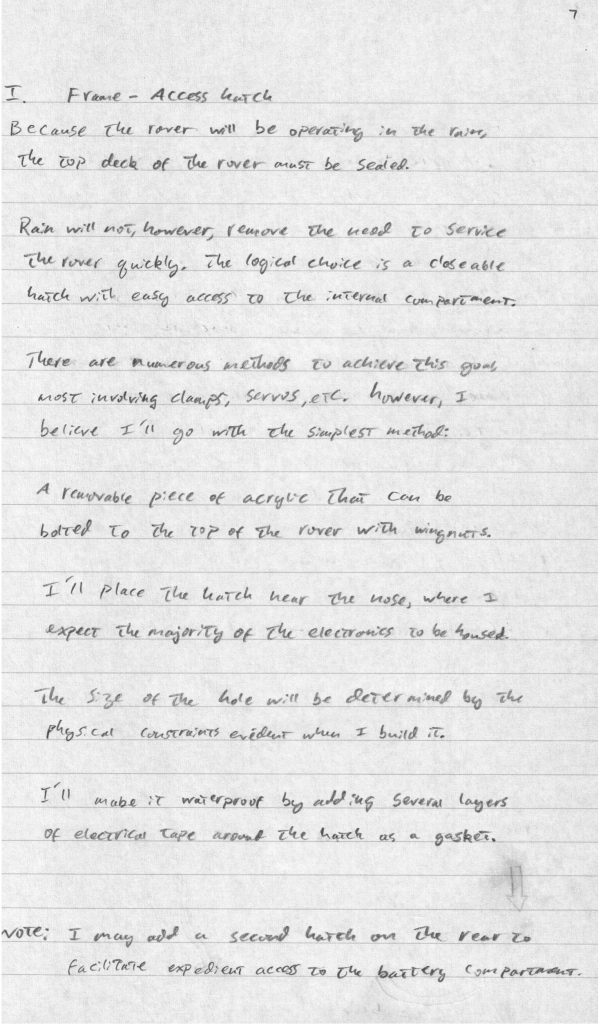
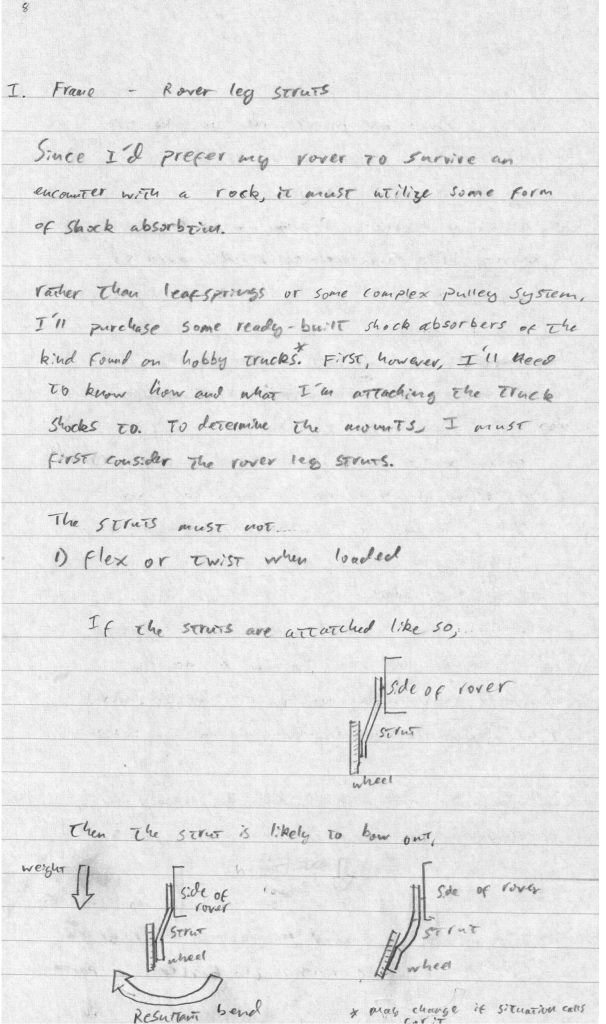
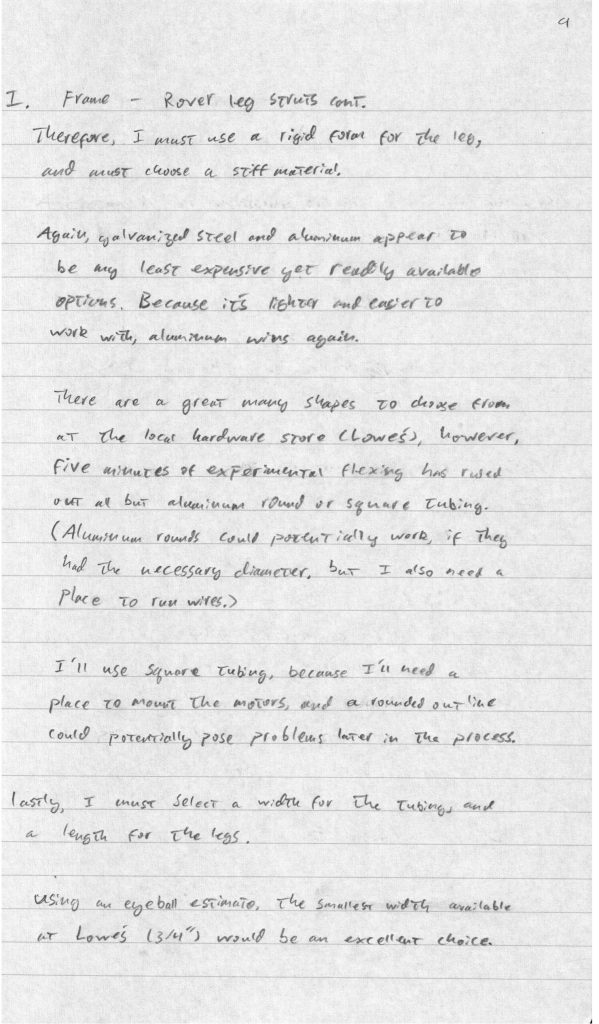
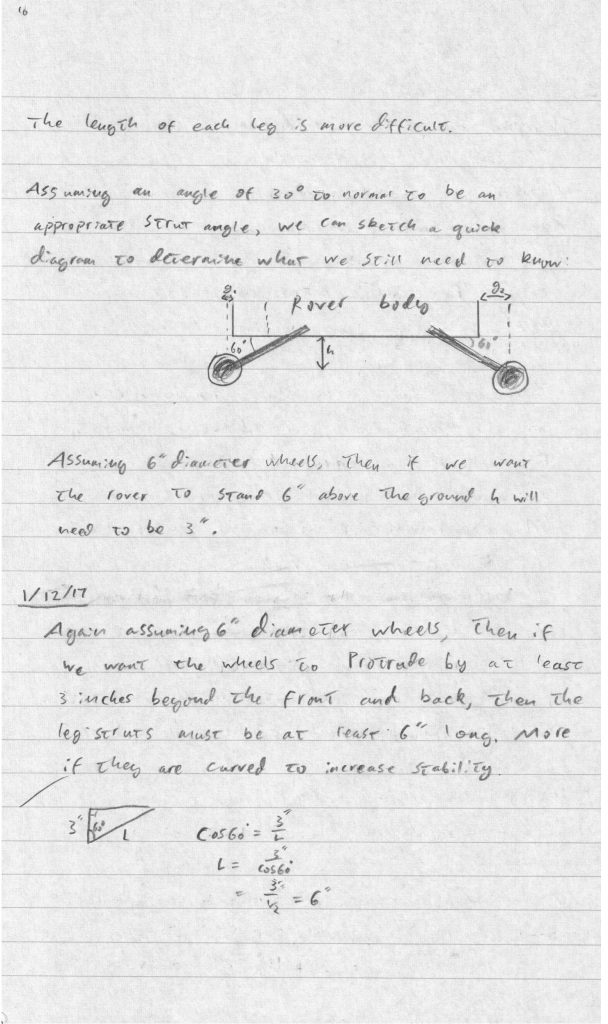
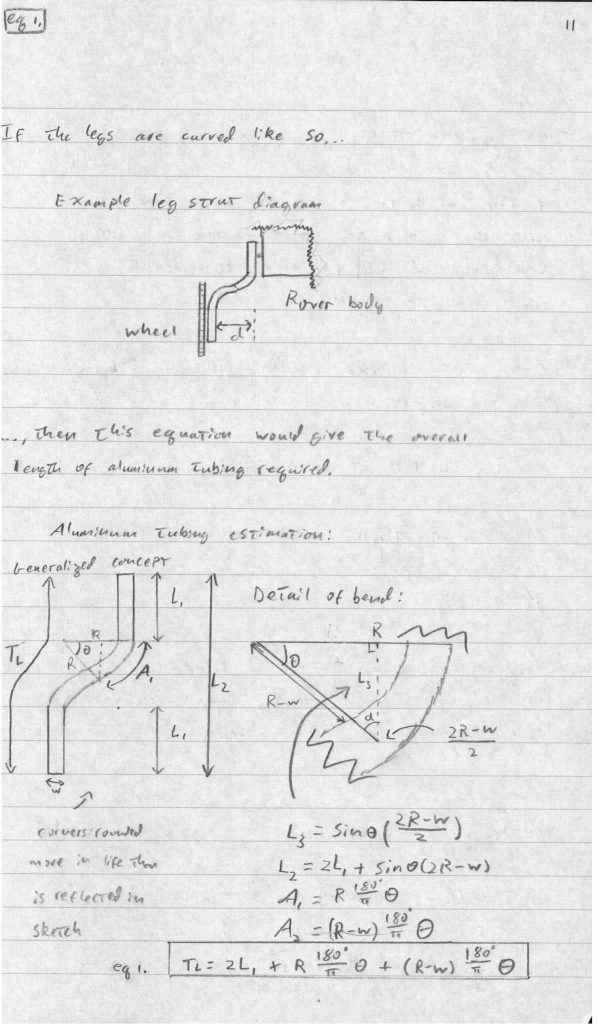
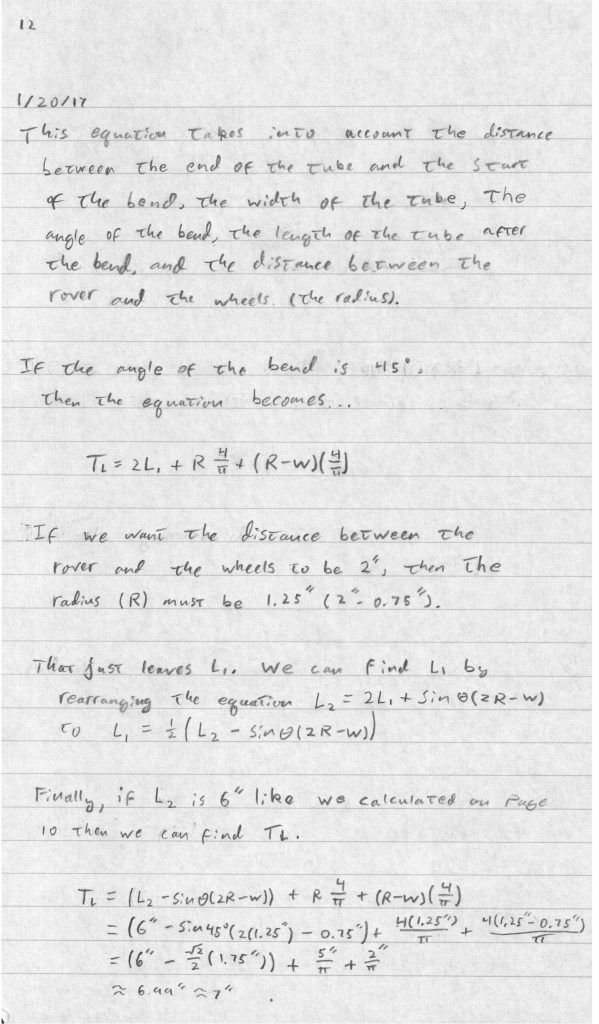
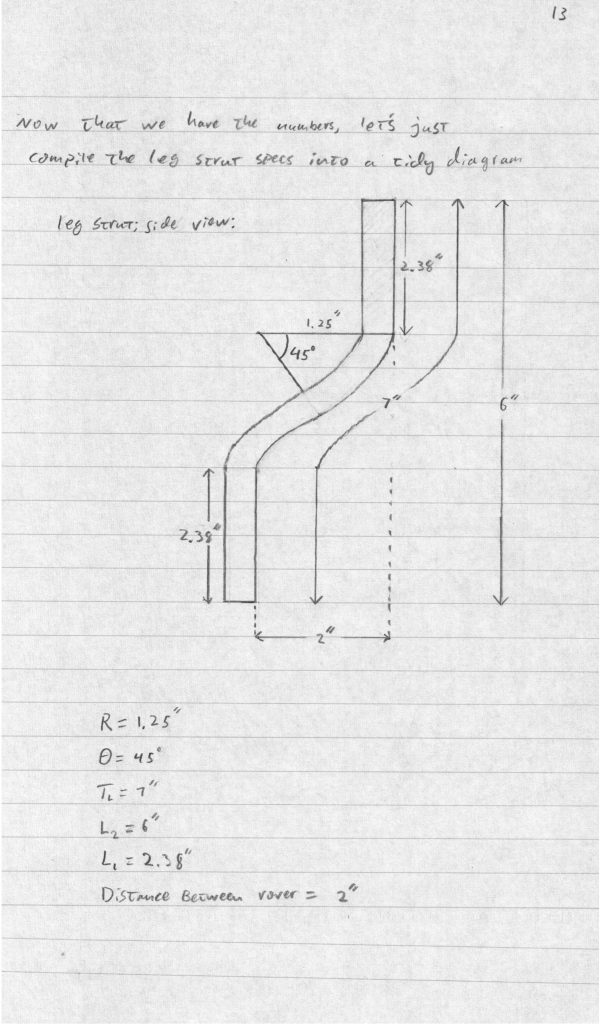
For the wheels, I’d already chosen to use some 6″-diameter wheels that I’d found on a hobbyist robotics website. They looked similar to the ones that my team (Area 42 Robotics) had used in our regional competition (2015? 2016?) where we won 6th place.
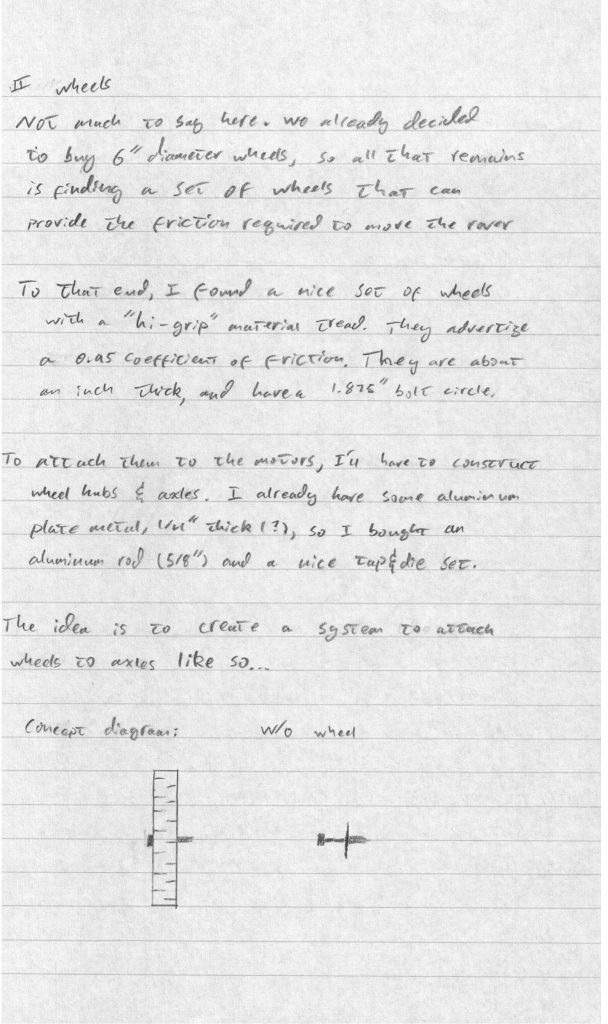
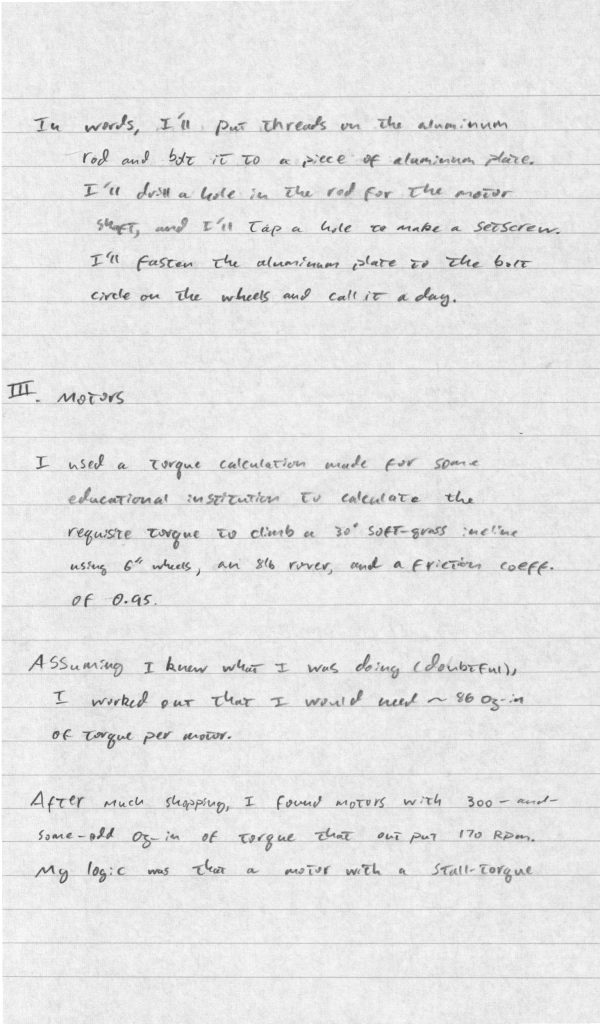
Since the rover was supposed to be rain-resistant, I first tried very hard to find true “waterproof” brushed DC motors. When I realized that I’d have a lot of difficulty finding motors like that, I decided to use normal gearmotors and put some waterproofing casement over them after-the-fact.
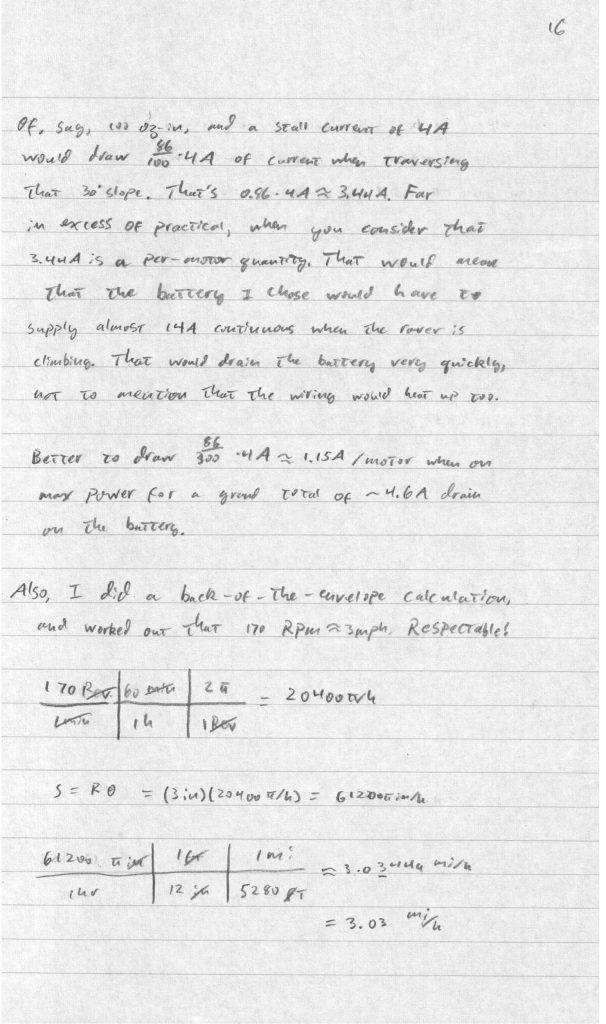
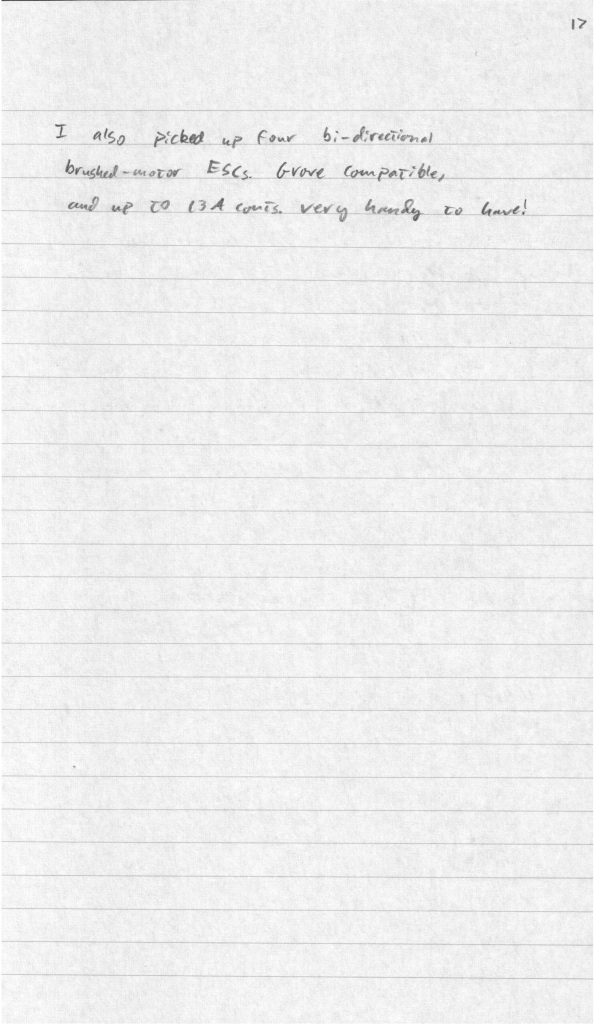
After this, I continued to work on the design but forgot to document it. I did build the rover, but I never implemented much control after the first few tests. I had elected to use tank-type steering for turning (opposite wheels turn in opposite directions), and the rover turned out to be too long for this to work effectively. As a result, it would follow a circle about ten feet in diameter when turning. This was simply too constraining, and it wasn’t an easy fix, so I abandoned version one and began considering a mark II version.
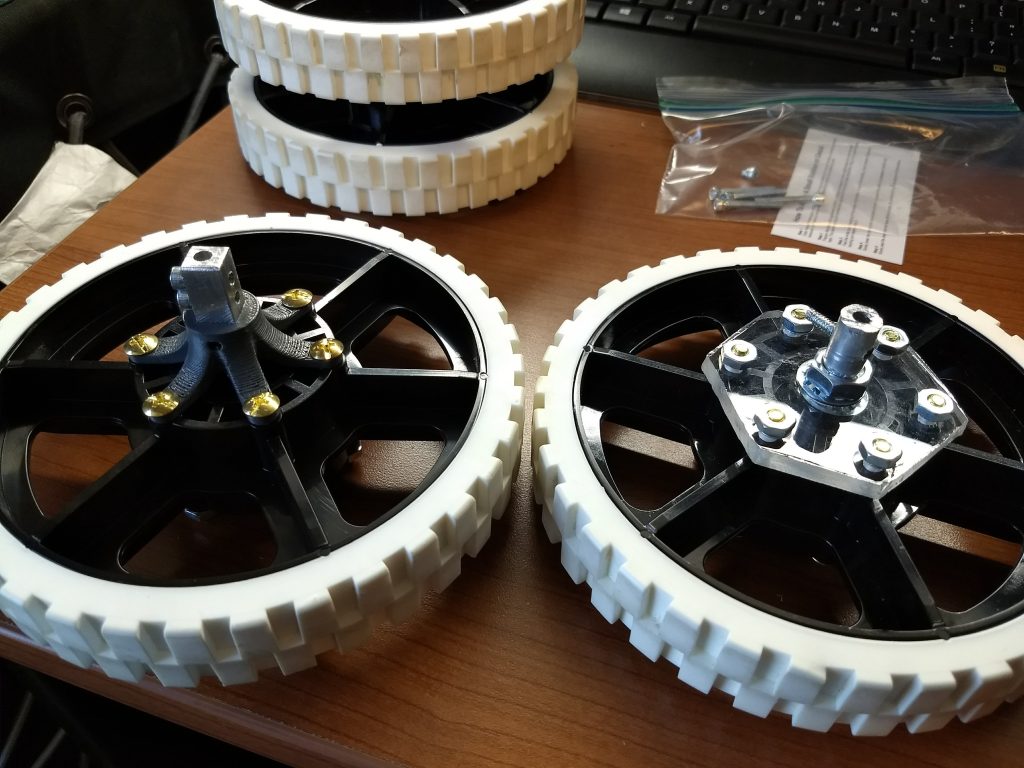